- Design, validate, and implement autoverification systems tailored to specific disciplines.
- Automate the acceptance or rejection of test results using predefined criteria.
- Involve key stakeholders, from IT personnel to IVD vendors, in the decision-making process for successful implementation.
Accelerating Towards Excellence: How One Cancer Care Center Used CLSI AUTO15 for Smarter Autoverification
The Situation
Case studies published by CLSI are solely intended to highlight and celebrate how laboratories and organizations are successfully implementing CLSI guidelines and standards in their unique settings. Inclusion in a case study does not constitute an endorsement, certification, or formal evaluation by CLSI. The practices and outcomes described are specific to the featured organization and may not be universally applicable.
Stanford Cancer Center South Bay needed a way to streamline the delivery of chemistry test results. The laboratory was facing growing challenges because of limited staffing, an increasing number of patients with complex needs, and a rising demand for faster turnaround times from medical professionals.
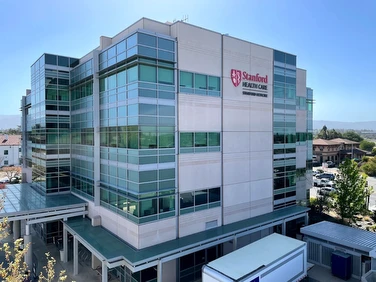
The Situation
Case studies published by CLSI are solely intended to highlight and celebrate how laboratories and organizations are successfully implementing CLSI guidelines and standards in their unique settings. Inclusion in a case study does not constitute an endorsement, certification, or formal evaluation by CLSI. The practices and outcomes described are specific to the featured organization and may not be universally applicable.
Stanford Cancer Center South Bay needed a way to streamline the delivery of chemistry test results. The laboratory was facing growing challenges because of limited staffing, an increasing number of patients with complex needs, and a rising demand for faster turnaround times from medical professionals.
Located in San Jose, California, Stanford Cancer Center South Bay is a comprehensive, multidisciplinary cancer treatment center known for its personalized care approach, tailored to meet the individual needs of each patient. Their testing services encompass everything from hematology to chemistry. These tests are crucial for monitoring a patient’s response to treatment, particularly when routine blood work is required to track progress and make critical adjustments.
Faced with increasing demand for faster turnaround times, a higher volume of complex cases, and limited human resources, the laboratory team at Stanford Cancer Center South Bay set out to improve their workflow and enhance test delivery. With intention and precision, they successfully implemented CLSI AUTO15 | Autoverification of Medical Laboratory Results for Specific Disciplines.
The Solution
This standard helped them establish a refined autoverification system, freeing up staff to handle more complex cases and deliver faster, more accurate, and more reliable test results. These changes also enabled health care professionals to have quicker access to vital laboratory data, allowing them to make timely, informed decisions and deliver high-quality, personalized patient care.
Elaborating on this successful implementation of CLSI AUTO15 is Ann Ho, CLS, MLS (ASCP) CM, Senior Clinical Laboratory Scientist at Stanford Health Care. Ann has been a dedicated laboratory professional with Stanford Health Care for nearly 10 years.
Ann shares how CLSI AUTO15 not only transformed the laboratory’s chemistry workflow but also strengthened the connection between laboratory excellence and patient outcomes at Stanford Cancer Center South Bay.
Why CLSI AUTO15?
With high demand, more patients, and a small laboratory staff, the team needed to find a quicker, yet safe and reliable way to deliver results without compromising the quality of patient care. The laborator
y turned to CLSI AUTO15 to help develop a more sophisticated autoverification system that could reduce the burden of manual review.
“Autoverification allows laboratories to use advanced algorithms and software to automatically validate test results based on defined criteria,” Ann said. “This process streamlines workflow and enhances efficiency, allowing the limited staff to focus on reviewing more complex cases that require human expertise.”
The standards outlined in CLSI AUTO15 are designed to guide laboratories seeking to automate the review of routine tests, ensuring timely reporting, which is crucial for care and treatment decisions.
Preparing for CLSI AUTO15
Stanford Cancer Center South Bay took a methodical, thoughtful approach to prepare laboratory staff, relevant stakeholders, and software for the proper implementation of CLSI AUTO15. Laying the groundwork for collaboration, testing, and training was key to a smooth and successful rollout.
“Following these steps allowed the laboratory at Stanford Cancer Center South Bay to effectively align with CLSI AUTO15,” Ann said. “These guidelines enhanced the efficiency and reliability of chemistry test results reporting, while ensuring high standards of patient care.”
The laboratory carried out several steps to ease all stakeholders into the transition:
- Assessment and planning were key to determining what was and was not working. The team began evaluating its existing laboratory workflows and protocols, which helped them identify areas that needed change or enhancement to meet standards. This step also included reviewing current autoverification practices and figuring out what types of tests could be automated.
- Staff training and education ensured that all stakeholders involved, including laboratory staff, understood CLSI AUTO15. Comprehensive training was provided on interpreting results, principles of autoverification, and the importance of quality control (QC).
- Establishing verification criteria was vital in developing specific information for autoverification. This included defining acceptable ranges for test results, criteria for flagging abnormal results, and protocols for manual review when necessary. One important aspect of this step was testing the laboratory information system (LIS) to ensure that chemistry results with delta check flags were assigned for manual review.
- QC measures, such as routine audits of the process, were implemented to monitor the accuracy and reliability of autoverified results.
- Validation of autoverification processes was conducted before going live to ensure set parameters worked as intended, catching outliers while smoothly autoverifying standard results.
- Go-live monitoring was followed closely after implementation. The team closely monitored system performance and made adjustments as needed, fine-tuning rules and thresholds for optimal performance.
- Documenting all changes was another crucial part of the transition, helping the laboratory demonstrate compliance with CLSI AUTO15. Documenting all procedure changes, training, and QC measures is essential for regulatory purposes and maintaining accreditation.
“An important factor for our laboratory to successfully implement CLSI AUTO15 was to involve all stakeholders by engaging laboratory staff, pathologists, and IT personnel in the decision-making process,” Ann said. “Their insights and experiences can help identify potential challenges and ensure that the chosen system meets the needs of all users.”
Outcome
Since implementing CLSI AUTO15 at Stanford Cancer Center South Bay, the impact on workflow has been significant. Routine chemistry results are now streamlined through a higher-quality autoverification system, significantly decreasing the turnaround time for results. Doctors receive test results faster, ensuring timely diagnosis and treatment plans for patients, which can lead to better health outcomes.
Image: Slow Turnaround Times Throughout the Day
(Provided by care team)
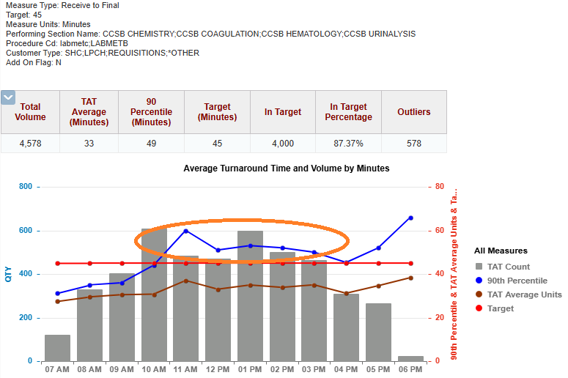
Image: Post-Implementation: Improved Turnaround Times and Higher Volumes Processed
(Provided by care team)
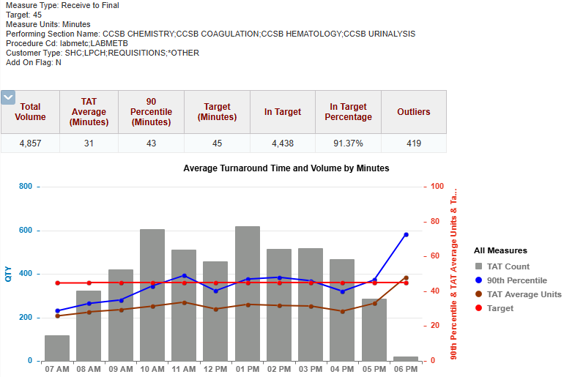
Impact
These improvements have streamlined the communication needs between medical practitioners and laboratory staff. The overall benefits also ensure more accurate and reliable tests, enhancing patient care.
Because of a more automated and sophisticated system, laboratory staff are also enjoying a lighter workload and can focus more on complex cases that require a higher level of human expertise.
“Overall, the implementation of chemistry autoverification processes has transformed laboratory operations, leading to improved efficiency, accuracy, and quality of care in our health care system,” Ann said.
In a high-volume, smaller-scale laboratory like Stanford’s, time and efficiency are crucial, especially when treating cancer patients with unique needs. Standards like CLSI AUTO15 not only enhance laboratory operations but also directly impact the quality and delivery of patient care and outcomes. Stanford Cancer Center South Bay’s case study demonstrates how a properly vetted framework can empower teams to innovate and collaborate, ultimately delivering the care that matters most.
“This improvement not only eases the pressure on the limited staff but also ensures that clinicians receive critical information more quickly,” Ann said. “This has led to better patient outcomes and more effective management of cancer care. The commitment to reducing turnaround times reflects the center’s dedication to meeting the needs of both patients and health care providers in a dynamic and demanding environment.”